Les opérations d’exploitation
Pour l’exploitation à ciel ouvert
L’abattage
Le choix de la méthode d’abatage dépend du type de roche, de ses propriétés physiques et mécaniques, des paramètres techniques des engins, des équipements miniers disponibles et des exigences de qualité du minerai extrait (propreté), ainsi que de la productivité de la mine.
Cette équipe de groupe de foration est sur chenille avec un marteau pneumatique hors du trou et récupération des poussières, il fore en moyenne des trous de mines de 3m de profondeur (la profondeur de perforation maximale= 15m).
La maille de foration de minerai = (1.5*1) donc 1.5 m2, celle de stérile est de 8 m2 = (4*2).
L’équipe de foration utilise plusieurs types d’explosifs et d’accessoires afin d’effectuer l’abatage à savoir : Explosif N30, Anfomil, Cordeau détonant 12g, Fil de tir, D.E.I (Détonateur électrique instantané), D.M.R (Détonateur à micro retard).
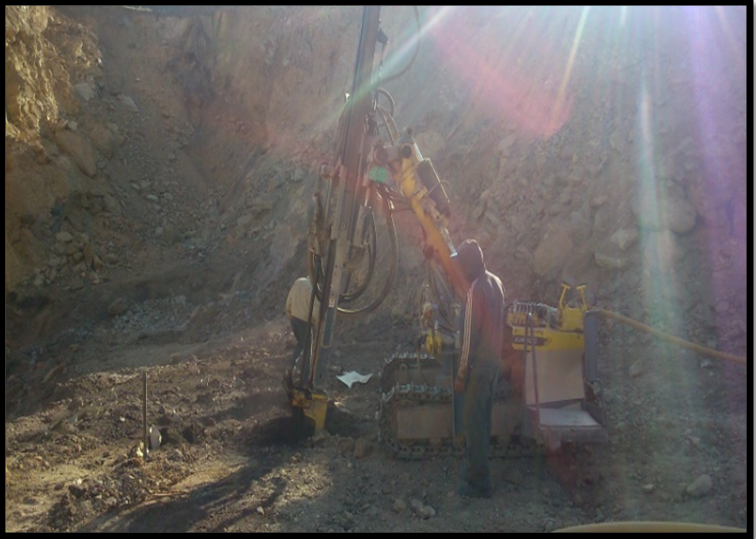
Le terrassement
Afin de nettoyer la piste après le tir, et de faciliter le travail des chargeuses et des Dumper, un bulldozer de type LIEBHER et d’une capacité de 2.3 m3 est utilisé pour le décapage. Actuellement, on dispose d’un Bulldozer de type LIEBHER.
A fin d’évacuer la matière de la plate forme de travail, la mine dispose pour le chargement de trois pelles chargeuses sur pneus; Chargeuse LG 959, Chargeuse VOLVO L120D et la chargeuse CASE.
L’ensemble de ces engins assurent aisément le chargement dans les trois secteurs du gite II.
Le transport de l’hématite et de roches stériles, est un des processus principaux dans la mine de Djebel Djerissa, et qui est le déplacement de la masse hématite des chantiers aux points de déchargement (Zones de stockages).
Etant donné les propriétés d’hématite et des roches stériles (calcaire, marne, argile, grès et sable), la mine a opté pour un transport par camion, à cet effet elle dispose actuellement de 3 Dumper en état de marche : deux dumper Caterpillar 730 et un ancien dumper D25D.
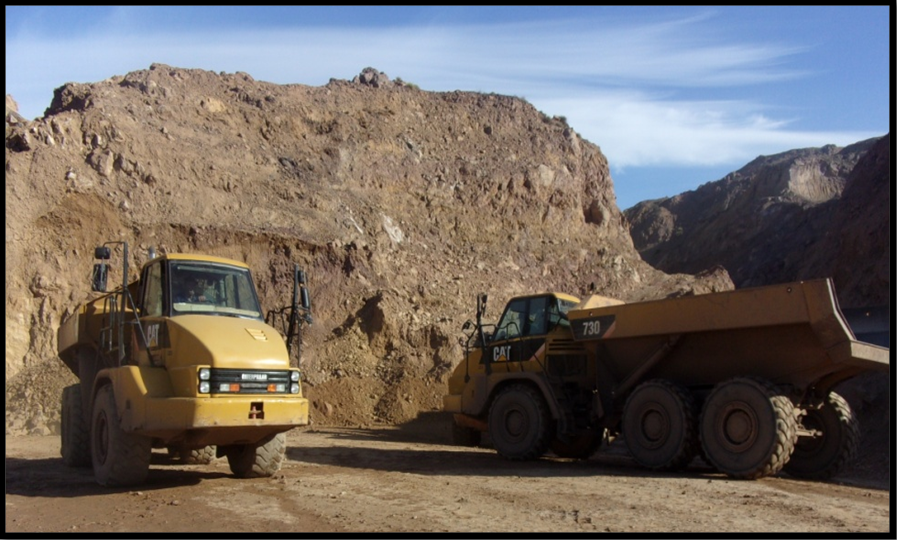
Pour l’exploitation souterraine
Exploitation sous terraine
Le traçage et l’abattage se font à l’explosif. La foration des trous de mines est assurée par des marteaux T21 avec un diamètre de 32mm et une longueur des trous de 1,60 à 2,40m. L’explosif utilisé est le Nitramite N30 en cartouches de 30mm de diamètre. L’amorçage est électrique avec des détonateurs à retard. Le chargement de minerai au front est effectué par des pelles chargeuses sur pneu. La desserte du minerai est assurée par des wagons tirés (photo-11) par une locomotive à gasoil (photo-11) dans les niveaux inférieurs et électrique au niveau du roulage principal. Un puits de 135m de profondeur relie les niveaux inférieurs au roulage principal assurant l’évacuation du minerai vers la recette principale au jour.
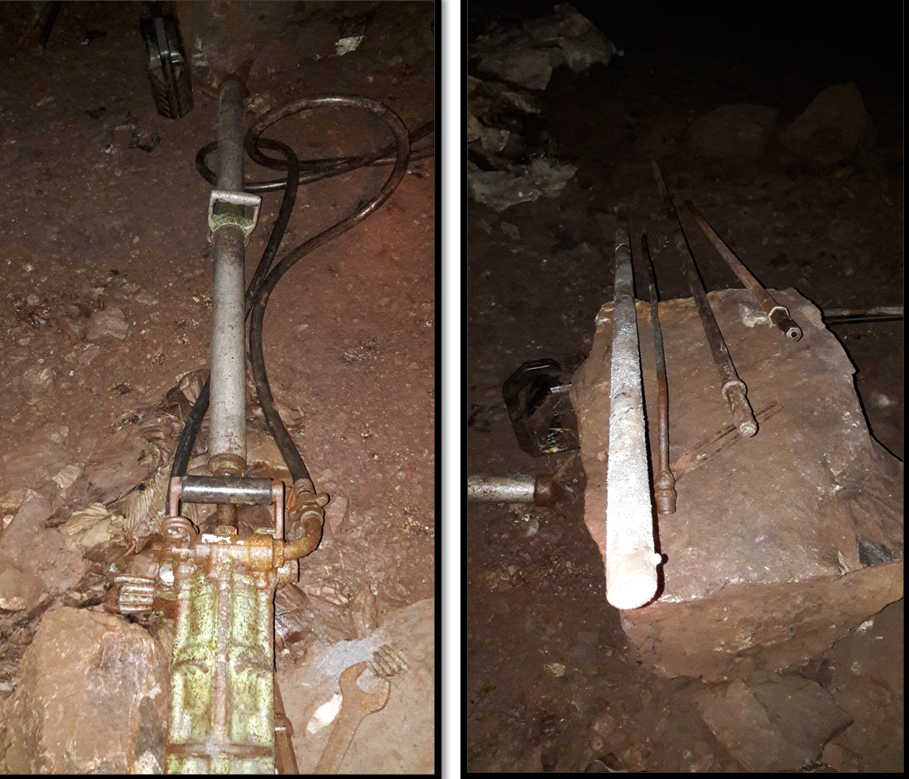
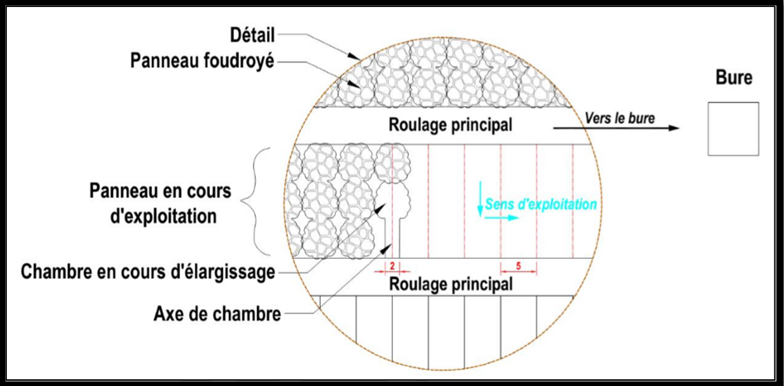
Exploitation des hématites (Oxydes de Fer)
L’exploitation d’hématite se fait selon la méthode dite des « sous-niveaux foudroyés » qui permet un taux de récupération de minerai d’environ 60%.
La méthode consiste à un découpage vertical du gisement par des sous-niveaux distants d’environ 5 m, qui sont reliés par des cheminées.
Horizontalement, le gîte est découpé en panneaux qui sont liés à l’une de ses extrémités par un roulage principal donnant accès au bure.
Perpendiculairement au roulage principal, des axes de chambres sont tracés tous les 5 m. Les chambres font 2 m X 2 m soit environs une section de 4 m².
Les sous-niveaux sont reliés par une rampe hélicoïdale donnant accès entre les niveaux 565 et 625.
Horizontalement, le gîte est découpé en panneaux. Entre deux panneaux successifs, un stot de protection (de 10 à 25 m d’épaisseur) est abandonné.
Au fond de ces axes de chambres, un élargissement des parements et du toit est pratiqué (de 1.50 m de part et d’autres et de 3.00 m au niveau du toit) jusqu’à toucher au foudroyage du niveau supérieur et des chambres avoisinantes déjà foudroyées. Dans cette étape, on pratique provisoirement la méthode des « chambres magasins » à savoir le maintien des minerais abattus du toit afin que l’ouvrier puisse monter sur le tas pour faire la foration du toit.
A la fin de l’exploitation des chambres, le soutirage des minerais abattus est effectué vers les cheminées de verses situées à l’extrémité des roulages principaux. Ensuite, la chambre est foudroyée par minage du toit restant et des parements.
Le minerai abattu dans les chantiers est récupéré par pelle-chargeuse, transporté vers les cheminées de verses qui débouchent sur les roulages 565 ou 625 puis acheminé par wagons à la station de culbutage au jour à travers le bure.
Les chambres et les stots séparant les panneaux semblent bien dimensionnés du moins en conditions normales (loin des anomalies géologiques). En effet, nous n’avons pas observé dans les chantiers visités des désordres en relation avec des concentrations de contraintes mécaniques au niveau des piliers ou des toits des chambres.
Le facteur critique dans cette méthode est le foudroyage du toit du gisement. D’après les exploitants, le foudroyage du toit du gisement suit normalement le foudroyage du minerai. Cependant, les anciens mineurs affirment avoir constaté des retards du foudroyage produisant deux configurations :
Exploitation des sidérites (carbonates de Fer)
L’exploitation des carbonates se fait selon la méthode dite des chambres et piliers abandonnés permettant un taux de récupération du minerai d’environ 40%.
La méthode consiste à un découpage vertical du gisement par des sous-niveaux distants d’environ 10.00 m.
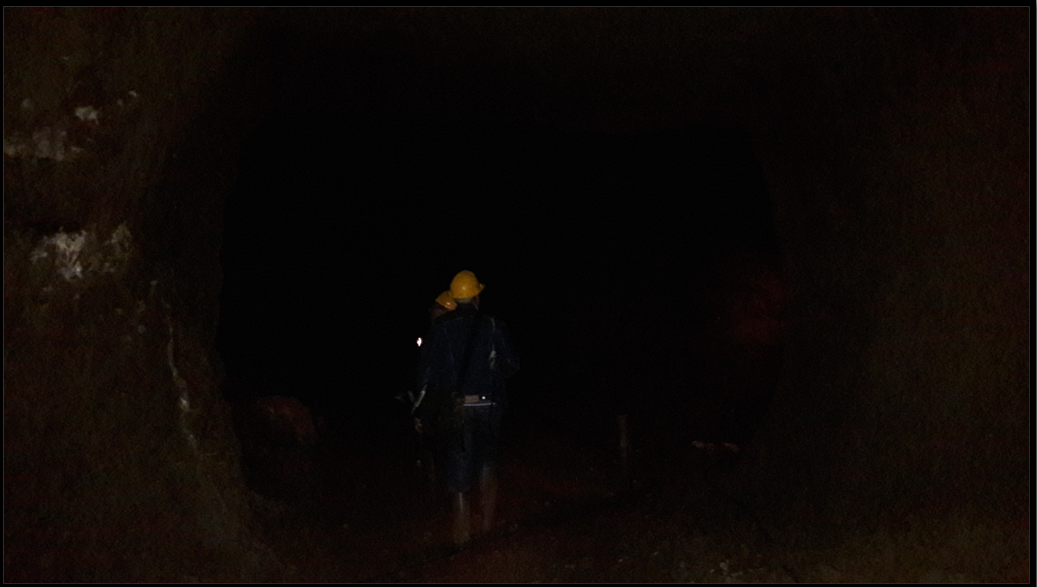
Chaque panneau est découpé par des galeries de section d’environ de 16.00 m² (4.00 m X 4.00 m) et distantes de 15.00 m (entre-axes). Ces galeries sont élargies par la suite à 9.00 m pour laisser des piliers de 6.00 m d’épaisseur (les galeries les plus anciens étés dimensionnées avec une largeur de 11.00 m séparées par des piliers de 6.00 m).
A l’extrémité de chaque chambre, une cheminée débouchant au niveau supérieur de la même chambre, est creusée. La cheminée sera élargie sur toute la largeur de la chambre (soit 9 m) par minage mécanisé moyennant une foreuse sur chenille.
Par la suite, la chambre est exploitée entre deux niveaux successifs par des mines verticales forés. Le minerai abattu sera récupéré au niveau inférieur par pelle-chargeuse et sera déversé dans les cheminées de verse creusées dans les stots de protection et sera récupéré au niveau 565 à travers des couloirs à ouverture pneumatique dans les wagons. Les wagons de capacité proche de 7.00 tonnes seront transportés au jour par locomotive diesel à travers le bure.
Dans cette configuration d’exploitation, les dimensions ultimes des chambres sont 9.00 m de largeur sur plus de 30.00 m de hauteur. Les toits des chambres reposent sur des piliers de minerai abandonné de 6.00 m de large sur plus de 30.00 m de hauteur.
Les opérations concassage
A l’arrivée au carreau de la mine (fig.11), les wagons chargés en minerai sont culbutés dans la trémie d’un concasseur à mâchoires. A la sortie de ce concasseur primaire, le minerai est convoyé sur une bande vers une station de criblage, une partie du minerai (granulat supérieur à 20 mm) est orientée vers un concasseur à marteaux. La déverse du produit fini (minerai à granulat 0-20 mm) est assurée par un convoyeur à bande.
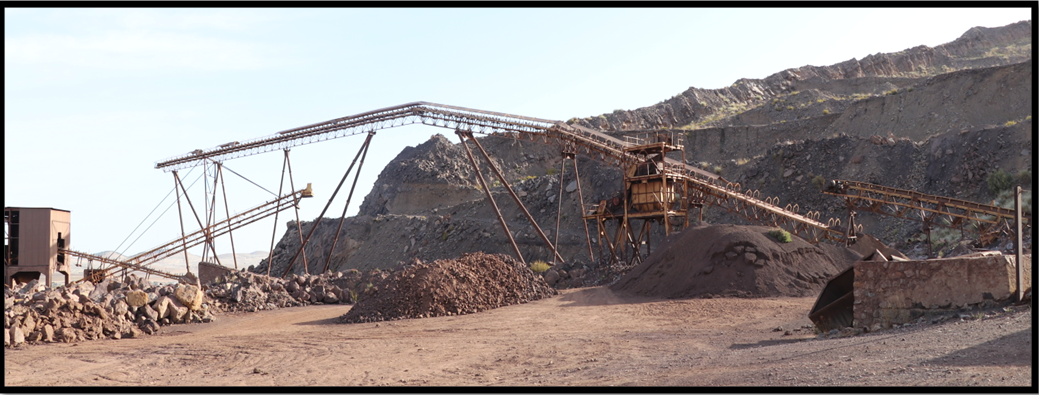
Station de concassage et de criblage